Game On
We reviewed competing heated grips on the market and identified a number of issues that we wanted to be sure to avoid. For example, we knew that the groove design they used allowed water to reach the circuitry underneath the rubber. Those grips can actually shock the user. Obviously, that’s no good. We also discovered that their cost per unit was high. So not only was the existing product on the market poorly designed, but it was expensive to make too.
First, The Design
We got to work. Our client wanted the grips to get really hot, really fast. We achieved this with a 12-volt system resistive heater. The grips are so powerful we included a temperature regulator in the design to make sure the grips don’t get too hot. Though it’s not just that simple. Because the grips can be used in temperatures as cold as -40°C, the design includes a feedback loop for temperature regulation. Our design measures the resistance of the heater traces itself and calculates the temperature based on that. It finds the surface temperature of the grip and uses that to determine the power output to give to the resistive heating element.
To make sure that the grips were up to our client’s specifications, we had weekly meetings where we got completely aligned on the design and vision for the grips and the bike. The client’s in control of what the final exterior looks like, we design what goes inside of it. Our molder worked directly with the client to make sure the technical design would fit well with the aesthetic design.
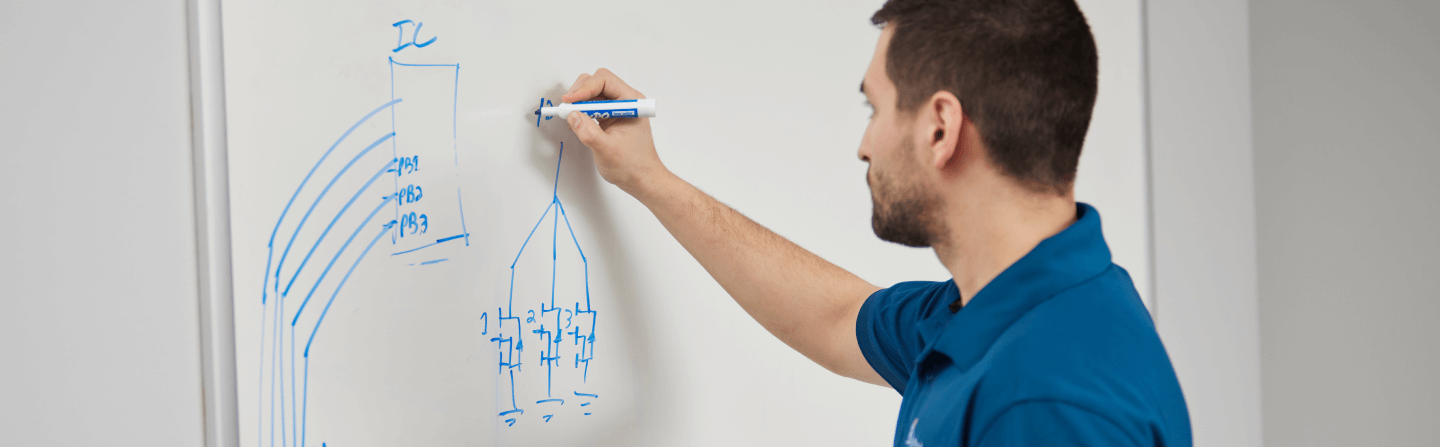
On to Manufacturing
We work with our manufacturing partners the whole time we’re doing design. Along the way through design, we have multiple checkpoints where we validate that what’s being designed can actually be manufactured. Once we finalize the design we have several production runs to ensure the product is manufactured up to quality standards.
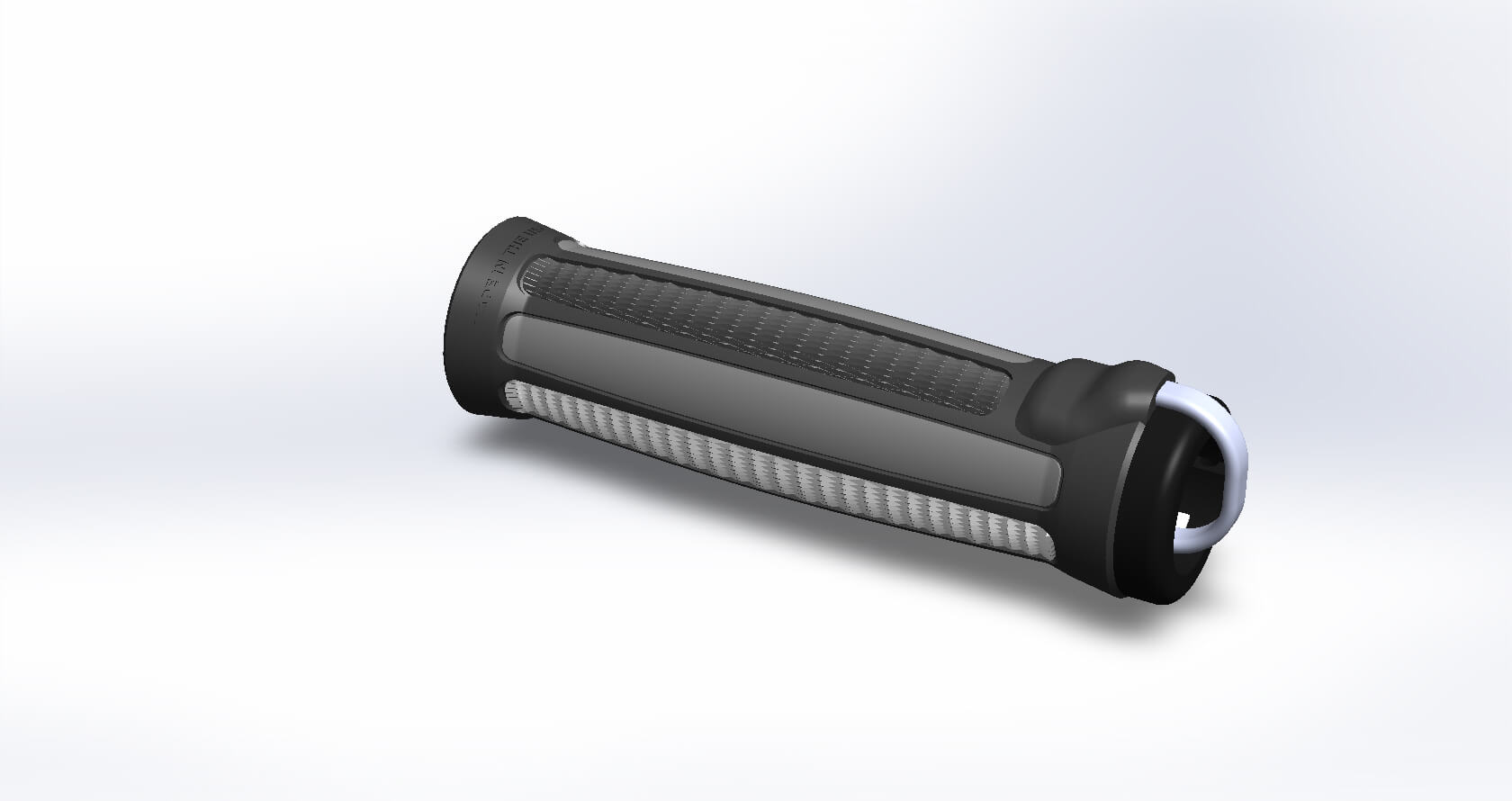